News Center
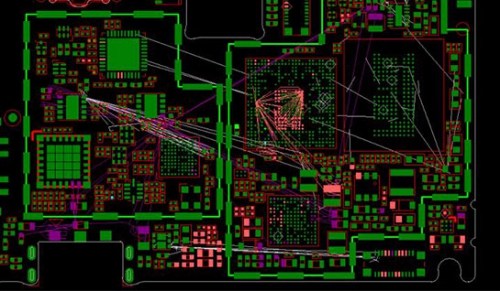
What is characteristic impedance?
Characteristic impedance:It is not a DC resistance, but a concept in long line transmission. In the high frequency range, the signal transmission process, the signal along the arrival place, the signal trace and the reference plane (power or ground plane) between the establishment of the electric field, there will be a momentary current.
If the transmission line is isotropic, a current I is always present as long as the signal is being transmitted, and if the output voltage of the signal is V, the transmission line is equated to a resistance of size V/I during signal transmission, calling this equivalent resistance the characteristic impedance Z of the transmission line.
During the transmission of the signal, if the characteristic impedance on the transmission path changes, the signal will be reflected at the junction where the impedance is not continuous.
Factors affecting the characteristic impedance?
The factors that affect the characteristic impedance are: Dielectric constant, Dielectric thickness, Wire width, and Copper foil thickness.
Solutions To Impedance Discontinuity Problems In PCB Design
1. Tapering line
Some RF component packages are small, SMD pad width may be as small as 12 mils, while the RF signal line width may reach more than 50 mils, so we need to use the gradient line, to prohibit abrupt changes in line width.
2. Corner
If RF signal lines at right angles, the effective line width of the corner will increase and impedance discontinuity, causing signal reflection. In order to reduce the discontinuity, the corner should be processed, there are two methods: tangent and rounded corners. The radius of the rounded corner should be large enough, in general, to ensure that: R>3W.
3. Large pads
When there are large pads on a 50-ohm microstrip line, the large pads are equivalent to the distributed capacitance, which disrupts the characteristic impedance continuity of the microstrip line. Two methods can be taken at the same time to improve: first of all, the microstrip line dielectric thickened, and secondly, the ground plane below the pad will be hollowed out, both can reduce the distributed capacitance of the pad.
4. Tenting Vias
The tenting vias are metal cylinders plated outside the through holes between the top and bottom layers of the board. Signal vias connect transmission lines on different layers. The vias stubs are the unused parts of the vias. The vias pads are circular spacers that connect the vias to the top or internal transmission lines. Isolation disks are annular gaps within each power or grounding layer to prevent short circuits to the power and grounding layers.
5. Through-hole coaxial connectors
Similar to through-hole structure, through-hole coaxial connectors also have impedance discontinuity, so the solution is the same as through-hole. The common methods to reduce the impedance discontinuity of through-hole coaxial connectors are the same: using diskless process, suitable wire exit, and optimizing the counter pad diameter.
Grande specializes in providing overall PCBA electronic manufacturing services, including PCB design, upstream electronic components procurement to PCB production and processing, SMT placement, DIP plug-in, PCBA testing, finished product assembly and other one-stop services.
The company gives full play to its competitive advantages in scale procurement and quality control, and has signed long-term cooperation agreements with many domestic and global electronic component manufacturers to ensure the quality and stable supply of raw material sources and transfer the benefits to customers.
Long-term procurement advantages in IC, resistors, capacitors, inductors, diodes and other components can greatly save customers’ inventory costs, improve production turnaround efficiency and save time. At present, we provide PCBA processing services for customers in USA, UK, Japan, Russia, France, Canada, Australia, Romania, Switzerland and other countries and regions.
We provide PCBA processing services, starting from PCB board fabrication, our own PCB manufacturer (with extremely strict TS16949 certification for the automotive industry), focusing on the quality of the board and PCBA quality control system.
Due to decades of experience in procurement of electronic components, we maintain long term cooperation with large brands to ensure the original packaging of components and procurement channels. In the encapsulation process of components, we choose Senju and Loctite solder paste to ensure the reliability of the soldering, with automatic printing machine, Panasonic high-speed placement machine, upper and lower eight temperature zone reflow soldering, AOI automatic optical detector, etc., which can effectively ensure the reliability and quality of the electronic packaging process.
In addition, the perfect management process of IPC, IPQC, OQA, etc., with clear job responsibilities and strict implementation of IPC electronic assembly acceptance standards. Regarding PCBA testing, we have professional engineers to perform 100% batch testing using various test stands, including pathway, noise, amplitude, signal, temperature, humidity, drop or execute customer’s detailed test program. All efforts aim to be a fine PCBA processing manufacturer.